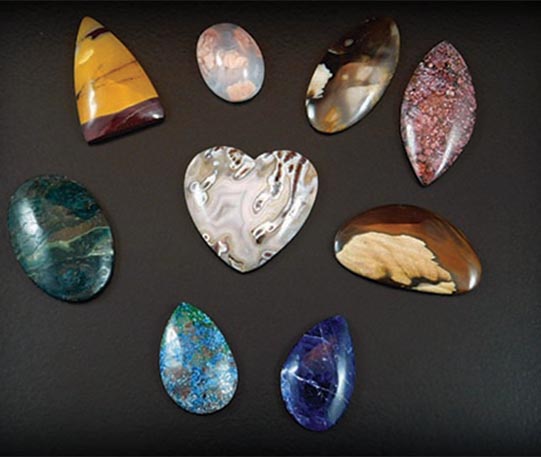
ADVERTORIAL
By Antoinette Rahn
Without a doubt, Michigan’s Upper Peninsula is a dream destination for many rockhounds, among other visitors. In addition to stunning geological formations, this region of the country features miles of Great Lakes shoreline with a variety of rocks and minerals, rock and mineral shops, natural science museums, and, it’s home to Kingsley North, Inc.
In the township of Norway, Michigan, just inside the western border of the Upper Peninsula, is where, in 1977 John Paupore Sr., founded Kingsley North. Since then, the Kingsley North company has continuously evolved and expanded to meet the needs and interests of lapidary and jewelry artists around the globe. Today the company offers lapidary equipment, tools, and supplies, beads, cabochons, findings, displays, and resource materials, among other items.
Many people cite Kingsley North as a go-to for quality tools, equipment, supplies, and service. Here you’ll find commentary from two talented metal and lapidary artists about their experiences using Kingsley North equipment.
Call: 800-338-9280 | Email: sales@kingsleynorth.com
Stop by in person: 910 N. Brown St., Norway, MI.
(M-F 8:30 a.m. – 5 p.m.; Sat. 9 a.m. – Noon)
Dig Discovery to Dynamic Design
Husband-and-wife jewelry makers, Doug and Cheryl Dole, are living the dream life of many creative individuals. They see to every step in the process of creating unique pieces of jewelry, from digging in the earth and acquiring specimens to transforming rough to workable lapidary material and finally, incorporating the stones into one-of-a-kind items of jewelry.
The joy of working together to create pieces of jewelry may be only matched by the Doles’ appreciation and interest in continually expanding their knowledge and lapidary skills. Learn more about these artists, who operate www.doledesigns.com, and the beauty they create, using Kingsley North equipment.
Rock & Gem: How long have you had an interest in cutting stone? How were you introduced to rockhounding and related interest such as cutting and polishing?
Cheryl Dole: We have been making jewelry as a husband and wife team for six years. My husband, Doug Dole and myself already enjoyed silversmithing, wire weaving, wire wrapping, and beading. We were buying our cabochons from various lapidary artist but had always considered cutting our own stone.
In early spring 2019, we took a trip to Texas to visit some friends of ours, both of whom are lapidary artist. They taught us their tips and tricks and we spent some time learning everything we could absorb. Once we returned from our trip, we knew we had to start getting our lapidary studio set up and begin buying equipment.
Armed with the new knowledge from our friends and an RV to plan rockhounding trips, we were on our way to a wonderful adventure in lapidary.
Creative Collaboration
R&G: How long have you been using the Kingsley North machine, and what influenced your decision to purchase this unit?
CD: While on our vacation we had the opportunity to use three different
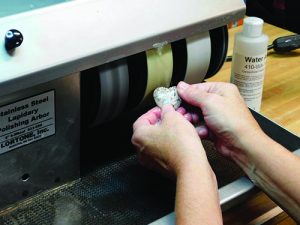
grinding/polishing machines, which was instrumental in making our ultimate decision to buy the Kingsley North Diamond Grinding/Polishing Machine. What we liked so much about the Kingsley North Grinding/Polishing Machine were the various ways that we could customize it to fit our needs. We received our equipment in late march of this year and have been non stop ever since.
R&G: What are two benefits you’ve discovered by using this piece of equipment?
CD: Being able to cut our own stone has helped us add another element to our jewelry designs. The ability to customize the Kingsley North Grinding/Polishing Machine has made making cabochons such and enjoyable process. We upgraded the wheels, and added a left hand disc, rubber base liner to protect the water pan, a larger water bin and a cerium oxide infused polishing disc.
R&G: How would you describe the experience of working with natural materials and your model of Kingsley North machinery?
CD: This piece of machinery has allowed us both to work as a team not only in our jewelry design, but in making the stone to complete the designs. While we both can individually do each process involved in making a cabochon, this machine allows us to do it together. Often times my husband will be using the first three wheels to grind trim and shape, while I put on the finishing touches with the last three wheels.
R&G: What are two valuable lessons you’ve learned from working with this machine?
CD: The lesson we have learned from working with this machine is that any original concerns we may have had about cutting and finishing our own cabochons have diminished. We have also learned that with a quality customizable Grinding/Polishing Machine, we can continue to improve the process making beautiful cabochons.
Next-Generation Artistry
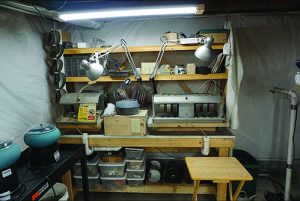
Rob Meixner’s introduction to what would become a passion and a profession came from his father. Working beside his jewelry-maker father in his Elbridge, New York shop, Meixner learned a lot about technique, design, and the importance of precision in jewelry making. Coupled with his father’s lessons about navigating his own life and artistry, it was a framework that has served Meixner well. Learn more about this precious metal and lapidary artist, who operates www.robmeixner.com, and chooses Kingsley North equipment.
Rock & Gem: How long have you had an interest in cutting stone? How were you introduced to rockhounding and related interest such as cutting and polishing?
Rob Meixner: My father was a rockhound, and I grew up hunting for rocks and minerals and going to rock shows. I have been a precious metal artist for 46 years, which is something I also learned from my father. Very early on, I started buying stones to incorporate into my jewelry, and I quickly realized I needed to learn to cut my own. About 40 years ago, I bought a Cabmate and started cutting.
The demands of a career and family took me away from it, and for a long time, I could only focus on metalwork. About 20 years ago, my career started to ramp down, and our kids left the house, at which point, I was able to take up lapidary again. This was also prompted by the fact that I had inherited about 1,000 pounds of semi-precious rock rough from my father. After retiring ten years ago, I built my first flat lap, and along with my original machine, I was back in business.
After a while, I realized that to cut the shapes and sizes that I wanted, I needed a bigger piece of equipment with plated and resin diamond media. After a lot of research and help from Kingsley North, I purchased their Lortone stainless steel, 6” six-wheel arbor kit.
Positively Challenging Self and Skills
R&G: How long have you been using the Kingsley North machine, and what influenced your decision to purchase this unit?
RM: I purchased my KN 6” arbor in November 2015. My decision was based on price, the desire to go to all diamond media, and a lot of research.
R&G: What are two benefits you’ve discovered by using this piece of equipment?
RM: Speed and accuracy.
R&G: How would you describe the experience of working with natural
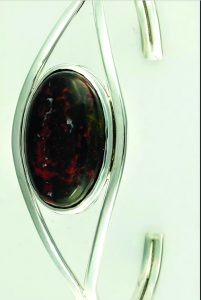
materials and your model of Kingsley North machinery?
RM: I use my KN arbor to cut and polish all types of rock and mineral material to incorporate into my jewelry. Sometimes the stone is designed to fit the jewelry, other times the jewelry is designed to fit the stone. I also use it to polish silver and hard resin. Once in a while, I even polish my hammerheads, mandrels, and other polished pieces of steel used to form metal. I wouldn’t be without it.
R&G: What are two valuable lessons you’ve learned from working with this machine?
RM: To use diamond media rather than silicon carbide and to use magnification as you work a stone because diamond media is very fast.