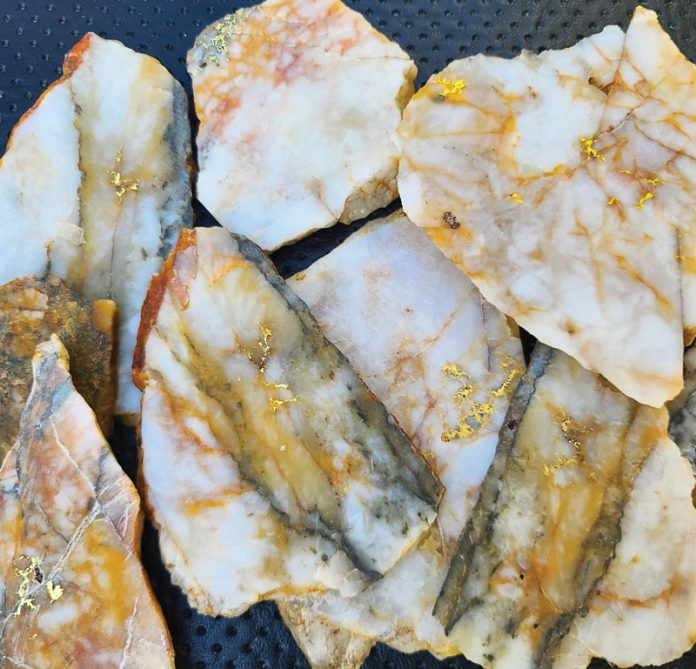
California gold doesn’t always come in nuggets. It can also be found embedded in quartz and used as a lapidary material.

A Golden History
California has always had a deep history in gold, ever since the 1840s gold rush, where thousands came from all over the world to try and capture their fortune in gold. Though you might not hear about the gold rush in California much anymore, it hasn’t stopped. New claims are being filed each year, and many tourists still come to try their hand at panning gold to get the real experience.
Finding Embedded Gold
Recently, Shannon Poe from the American Mining Rights Association (AMRA), and his partners have been digging in the Screamer Mine near Angels Camp, California. Much of the gold there is embedded in large quartz specimens and it cannot be seen by the naked eye. They have uncovered quite a bit by using metal detectors and then bringing the material back to their shop and slabbing the rocks to see the gold veins run through the center of the quartz. The gold can then be run through the extraction process, or it can be utilized as lapidary-grade material. The slabs containing gold veins can be performed to design cabochons.
Tips For Working With Gold-Embedded Quartz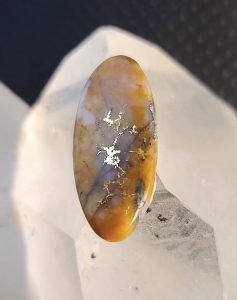
Although quartz isn’t very complex to work with, adding gold to the mix changes a few things in your setup. To start, quartz and most California materials are generally fractured and can easily fall apart at any time during the lapidary process. Stabilizing the material first is beneficial to ensure getting the most material to work with, without losing any from it falling apart either on the saw or when starting to grind performs.
Next, when cutting the quartz down, use the thinnest blade possible so that you waste very little of the gold content. At this point, you want to inspect all your slabs to ensure the stabilization process effectively filled any fissures in your material and that it will be solid enough to proceed to cab it. If there are open cracks, send it back for a second stabilizing treatment. At this point, be ready to trim out the cabochon preforms.
Cabbing the Quartz
Cabbing gold-embedded quartz adds a little more setup to your machine. This is where you want to completely clean out your cabbing machine and add material to the floor of your bays. Felt is a good option, it will allow the water to pass through it while it gathers all the grinding particles as you shape your cabochons. This way no gold is being wasted. It can be collected and processed at a later time.
Start the cabbing process on an 80-grit steel wheel. Cautiously grind the shape and dome. Continue to check often, as you never know how much gold will be in any area of the material and you don’t want to grind it away. Once the shape is complete, either uses a 140 or 220 soft resin diamond grit wheel to smooth it and remove any remaining scratches left from the course steel wheel.
From this point, continue to the 280 soft resin wheel, and continue to dry it off every so often to ensure all the scratches have been removed. The rest of the way is rather routine, from the 600 grit, all the way up to the 14k grit wheel. Once you’ve finished on the 14k grit wheel, it will be beautifully polished and not much else is needed but maybe a quick polish with either jeweler’s rouge or Zam with a felt tip Dremel bit.
This story about California gold previously appeared in Rock & Gem magazine. Click here to subscribe! Story by Russ Kaniuth.