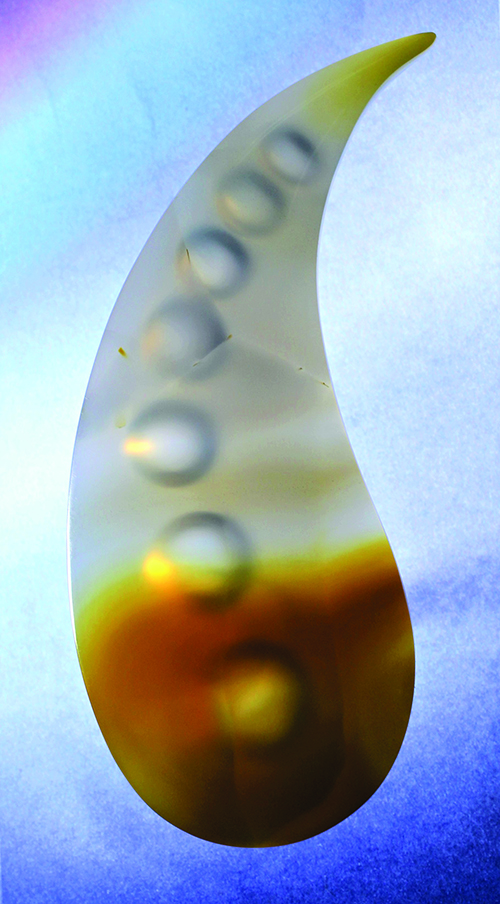
By Bob Rush
Recently I have created random patterns when I carved the holes in the back of a cab. For this month’s project I decided to do a geometric pattern with graduated size holes. I started with selecting a slab that had some differing colors with no definite pattern. It did have some internal clear distortions that were created during the formation of the material.
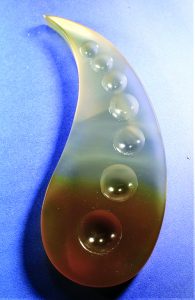
I went back to one of my favorite shapes – a curved teardrop – to design the piece. Past patterns of the cab had a gentle inside curve that fit the diameter of my 8” diameter grinding and sanding wheels so grinding and sanding the curve were quite easy to accomplish. On this piece I increased the inside curve significantly and it mandated a different method to grind and sand the curve. I fell back to my usual method of using a 1” Mizzy silicon carbide grinding wheel. These wheels are designed to be used dry. I like using them because I can access areas where bigger wheels will not reach. Their use mandates wearing of respiratory protection suitable for your particular respiratory health. They grind rather quickly and aggressively, and you do not have water obscuring your progress.
Though the Mizzy wheels work quickly they do not leave a smooth surface so considerable sanding efforts are needed to get a polishable surface. I have changed from using silicon sanding paper to using silicon carbide sanding blocks that I introduced in past projects. I started with the flat side of a 220- grit soft binder block. By holding the carving block parallel to the previously ground surface and pushing it at an oblique angle into the curvature the sanding can be quickly accomplished. I repeat this with a 400 and 600- grit blocks to finish the sanding.
The height of the cab is 3-3/4”. I used a 3-1/4” diameter circle template to lay out the location on the back of the cab for the diminishing sized round holes. I spaced the largest holes further apart and reduced the distance between them as the holes got smaller.
The sets of diamond ball burs that I use are graduated in size from large to small, but the sizes are not marked on each bur, so I have to measure each one with a caliper to ensure that the ones I use are a consecutive amount smaller than the last one used.
I drilled the holes with a 36-grit bur to within 4mm from the front surface of the cab. I finished the grinding with a 220-grit bit and finally a 400-grit one. Polishing involved making small wood burs using a coarse file shaped to fit in the holes. You do not have to make a wood bur for each size of hole. A smaller bit will polish a larger hole. I made 4 different sizes bits including one small enough for the smallest hole. As I have mentioned before I used cerium oxide mixed with water to a heavy paste to polish the holes.
When viewed from the front the smaller holes at the top of the cab have a sideways oblong appearance due to the higher dome curvature of the cab at the curved point.