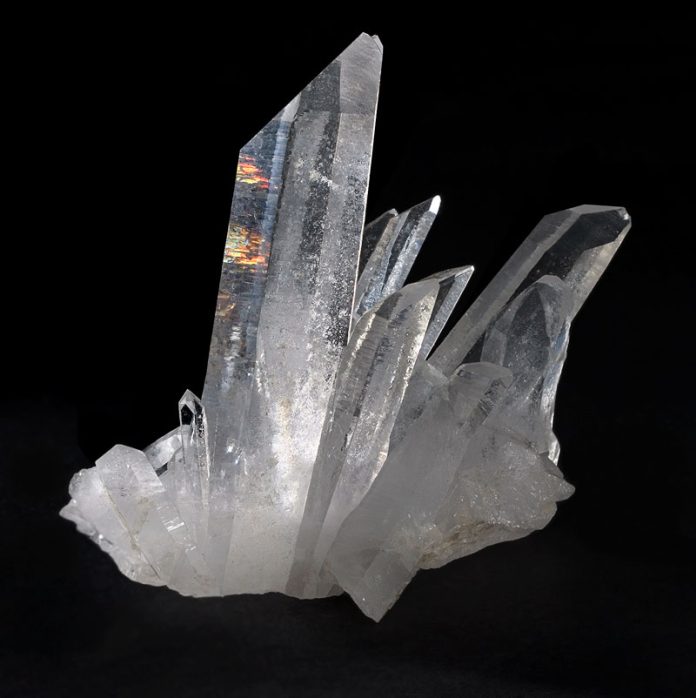
Synthetic quartz, born from the union of scientific ingenuity and natural beauty, has revolutionized the world of gemstones and industrial applications alike. My favorite paperweight is a six-inch long, two-inch-thick quartz crystal. Its water-clear transparency lacks common inclusions in quartz that can be used when wondering how to identify quartz. It is reminiscent of fine Arkansas rock crystal. However, the crystal’s brick-like shape, mold-patterned surfaces and beveled ends reveal its true identity: a synthetic crystal that was grown in an autoclave at New Jersey’s AT&T Bell Laboratories (now Nokia-Bell Labs) about 30 years ago. This brings up questions like are synthetic diamonds real? Is synthetic quartz real? Yes. But these crystals are formed with human help.
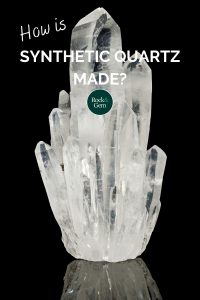
German geologist Karl Emil von Schafthäutl first synthesized quartz in 1845 using a silica solution and a laboratory vessel similar to a modern stovetop pressure cooker. Although von Schafthäutl’s tiny, synthetic crystals represented a significant scientific advancement, they had no commercial value, since quartz had few technological applications at that time.
French physicists, Pierre and Jacques Curie discovered the first of quartz’s remarkable electrical properties in 1880. By applying mechanical stress to quartz crystals, they generated an electrical potential (voltage) across certain crystal faces. The physicists named the effect “piezoelectricity” after the Greek piezein which means “to press.” The Curies next learned that applying electrical current physically deformed quartz by altering its crystal-face angles.
In 1918, other researchers discovered that thinly sliced quartz “wafers” vibrated mechanically at a natural resonance frequency of 32,768 cycles per second when conducting electrical current. The emerging current was regulated precisely to that frequency.
Several years later, Bell Laboratories scientists designed a quartz oscillator to control a clock with unprecedented accuracy. This discovery triggered a rush for a rare, special type of natural quartz—single, not twinned, “electronic-grade” crystals with undistorted crystal lattices large enough to be cut into small, thin wafers of various sizes.
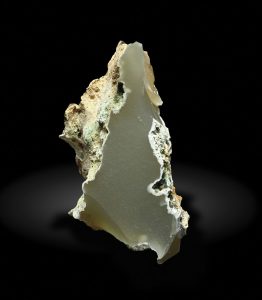
Wikimedia Commons
Quartz wafers were soon regulating both time and electrical frequencies in chronometers, radios, radars, bombsights and many other instruments. But natural, electronic-grade quartz came only from Brazil and, to a lesser extent, from Arkansas. During World War II, natural, electronic-grade quartz crystals were designated as a strategic material, while scientists in the United States, Germany and Japan raced unsuccessfully to develop a commercial synthesis process. By 1950, the synthetic, electronic-grade quartz crystals that could be reliably produced were still too small for most applications.
In the late 1950s, as demand for electronic-grade quartz boomed, researchers finally commercialized a method to grow large quartz crystals. This hydrothermal process is similar to the formation of natural quartz and is still used today.
In quartz synthesis, a powdered, natural, high-quality (but nonelectronic-grade) quartz called “lascas” is mixed with an aqueous solution of basic sodium carbonate, then placed in high-temperature, high-pressure, steel autoclaves. Seed crystals—thin sheets cut from electronic-grade quartz, either natural or synthetic—are suspended from the top of the autoclave, which is then sealed and heated from the bottom to 400° C (742° F) in pressures reaching 30,000 pounds per square inch.
The lascas dissolves into a silica-rich solution that rises by convection to the cooler, upper section of the autoclave where it becomes supersaturated and crystallizes onto the seed-crystal surface. Through closely controlled convection flow, temperature and pressure, the growing synthetic quartz crystals develop electronically perfect lattice structures. After about 80 days, the synthetic crystals are removed and cut into tiny wafers.
Today, about 300 metric tons of lascas are mined each year and converted into 225 metric tons of electronic-grade synthetic quartz worth about $40 million. More than 10 billion tiny wafers and oscillators are produced worldwide each year.
Most are used in electronic applications such as computers, cell phones, radios, navigational devices and digital games.
When doped with iron and manganese chromophores, autoclave silica mixes yield synthetic citrine and amethyst, which are then faceted and sometimes passed off as natural gems.
Lascas is mined in Brazil, Madagascar and Canada, while China, Japan and Russia manufacture most of the world’s electronic-grade synthetic quartz. The United States has imported its entire supply of electronic-grade synthetic quartz since 2003.
My desktop crystal is an attractive and unusual reminder of the remarkable electrical properties of quartz, both natural and synthetic.
This story about synthetic quartz previously appeared in Rock & Gem magazine. Click here to subscribe. Story by Steve Voynick.