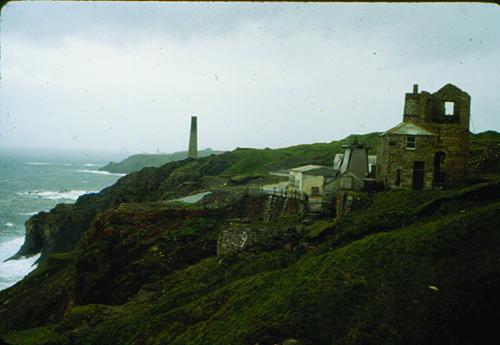
Mining in Cornwall, England had an impact when hard rock mining began in America with miners from all over the world arriving and bringing with them the knowledge and mining skills learned and shared over the centuries.
German miners were recognized as the more skillful miners in part because mining had its beginnings in Germany over 1,000 years ago. Their advanced mining skills were revealed in the 1850s text, De Re Metallica (On the Nature of Metals), written by George Bauer and translated in modern times by Herbert Hoover, and his wife Lou. This book, the first to reveal the secrets of mining, was referenced by mining people into the 20th century. Also, it was German miners who were brought to England to help unskilled farmers develop the skills and machinery needed for mining in Cornwall, England where mining copper and tin were pursued after harvest time.
German Miners’ Early Aid to Cornwall
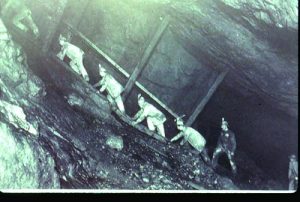
Some evidence shows earlier in history, the Phoenicians were in England — a place they called Cassiterides — in search of tin. Such visits encouraged locals to gather heavy, black tin oxide rocks from local streams. This eventually led to mining in Cornwall, England where miners worked near-surface veins found in and around the cliffs of Cornwall. As hard rock mining developed, and locals were trained by German miners, Cornwall, England slowly emerged as a source of copper and tin.
By the 1700’s Cornish miners, called “Cousin Jacks”, had solved many of the earlier mining problems, and were considered some of the best at extracting ore. Their skills were in demand all over the world. The name “Cousin Jack” came about when developing mine companies would need help mining in Cornwall, England. Cornish miners would invariably suggest they had a “Cousin Jack” miner back home.
You have to realize hard rock mining 600 years ago in Europe was fraught with problems. It was brutal and slow work, requiring great human effort. There was no steam for power, only water wheels with limited motion. Everything was done by hand. Even when gunpowder was introduced to mining in Cornwall, England, there were problems. It was explosive and unpredictable. How could someone safely ignite gunpowder?
As miners dug deeper into the earth, groundwater became a major challenge. There was no easy way to remove water and hoist ore to the surface except with muscle power. Even the crushing of ore was crude. It was common practice for women to break up the boulders of ore with hammers so it could be smelted.
Mining in Cornwall, England: Demand Prompts Improved Techniques
As the demand for copper and tin in England increased, so did the need to improve the techniques of mining in Cornwall, England. And it was Cornish miners and English inventors who developed a series of techniques and machinery that led to England’s Industrial Revolution. These skills became recognized across the world. For example, the first important copper mine in America in Bristol Connecticut, used Cousin Jacks in the early 1840s, preceding production from the great copper deposits in Northern Michigan.
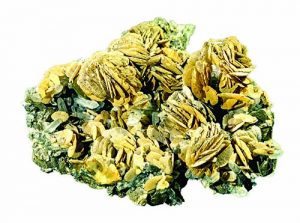
A significant problem shared by all mining operations, regardless of location, is breaking the metal-bearing rock in quantity to meet demand. The earliest method for cracking rock so it could be mined involved fire. Set a big fire against the rock face of an ore vein and once the rock was hot enough, douse it with water or wine to cause it to shatter. However, fire only penetrated a little into the rock while filling the air with noxious fumes. At the time, mining was slow going, limited in production and the lives of miners were short.
Gunpowder Discovery Brings Changes
Fortunately, 9th-century Chinese alchemists searching for the elixir of life accidentally discovered gunpowder. But gunpowder was a two-edged sword. It shattered much more rock, but once packed into a drill hole how could you ignite the gunpowder without it blowing up in your face? Miners tried all sorts of fuses — homemade unpredictable fuses like gunpowder in a goose quill. If gunpowder got wet you could not accurately time an explosion, and water was always an issue. It was as though miners had a tiger by the tail and suffered from it. Wet gunpowder in the drill hole would not burn or burn slowly, thus exploding later than expected, and any spark or excess heat could ignite it. Miners had to use wood tamping rods and such to pack drill holes, and even then gunpowder might ignite killing or maiming anyone nearby. This was the state of mining in Cornwall, England during the 1700s and 1800s
Bickford’s Fuse
Then along came English inventor William Bickford. In 1831, Bickford developed the first dependable fuse that solved the problem of igniting gunpowder. It helped avoid pre-ignition and gave miners a reliable explosion.
Bickford’s fuse was a long slender tube of gunpowder made in any length wrapped with string-like organic fibers called juke. Additionally, the entire length of the fuse was coated with tar to protect it from water. The fuse could be bent and cut into measurable lengths. A one-foot length of Bickford fuse would take about 30 seconds to burn. It was slender enough to fit into a drill hole and still give miners a chance to reach a safe place before discharge. The Bickford fuse was the universal choice of miners, even with the appearance of dynamite in the 1850s. Bickford’s fuse made it possible for faster, more efficient ore removal and extended mines ever more deeply, except for that other problem, water.
Steam Pump Changes Mining in Cornwall, England
England is not exactly a desert region, and early German miners used water wheels set up at various depths within the mine, to raise unwanted water to the surface. Water wheels are limited in their ability to lift water, and the deeper they are in a mine the more difficult they are to operate. Plus, horse whims, which were used to reel buckets on a rope, were ineffective at depth.
An alternative method, which was developed by Englishman Thomas Savery, was the ‘Miner’s Friend’ steam pump. This device used steam to lift water out of mines, using a complicated system of pressure and vacuum. The problem was it wasn’t much better at lifting water than a water wheel.
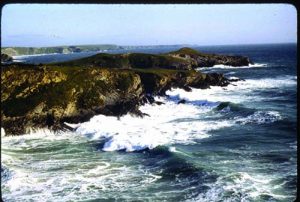
This steam pump could only manage to push water some 30 vertical feet. To work at depth, it would take several ‘Miner’s Friends’ working in sequence to overcome gravity. Even if this was the solution, what were the miners to do about the gases that were produced as a result of burning coal to create the steam?
This serious problem was resolved when Savery and Thomas Newcomen worked together to develop the Newcomen engine. This more powerful steam engine and pump was the answer to removing water from hard rock and coal mines. A single Newcomen steam powdered engine could raise water 300 feet. With later developments, these machines made water removal from deep mines possible.
Origins of the Walking Beam Engine
Newcomen called his engine a beam engine. In the U.S., such a mechanism is referred to as a walking beam engine. These engines are a common sight in oil fields. This type of engine involves a large metal beam that rocks back and forth on a single fulcrum. One end is attached to a power source, and the other end works a pump rod that extends down into the earth to depth. The pump rod can be several hundred feet long. With each stroke from the powerful device, now operated by electricity, the walking beam rocks down and the pump rod drops deeper into the ground. On the upstroke, water or oil is lifted toward the surface, and a series of valves control the upward direction of flow.
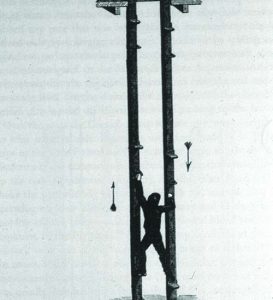
As more and more efficient steam-powered pumps were developed, the beam engine was used on every mine developed in Cornwall and other English mines. Among the stark features of the Cornish countryside today, is the many lonely, crumbling brick engine houses and chimneys that once housed the power and beam engine mechanisms of an active mine.
Deteriorating Miner Health
Another of the significant and far-reaching problems that quickly appeared in Cornwall was the deteriorating health of the miners. In fact, in the time of major mine production in Cornwall for a Cornish miner to live beyond the age of 40 was an exception. All miners suffered from ‘consumption,” an undiagnosed and crippling lung ailment. As mines reached hundreds of feet into the earth, miners worked in a wet and foul atmosphere of a mine tunnel. At shift’s end, exhausted miners faced the arduous climb up several hundred feet of ladder to exit the mine, only to emerge into the wet, sometimes bitterly cold wind blowing in from the Atlantic Ocean. No wonder so many miners became crippled or succumb to lung problems.
The hazards to miners’ health became such a problem the English Crown offered a substantial financial award to anyone who could solve this fatal problem. Little did the government realize a partial solution seemed to exist within the mine itself, and it was the miners who figured it out. The idea was to eliminate the exhausting climb from the interior of the mine to the surface.
Makeshift Measures Help Miners
The main shaft of any mine often had one and sometimes two, big pump rods that lifted and dropped, rocking up and down all day and night, as long as the beam engine was working. Some enterprising miner realized by placing small platforms on the pump rod it could lift someone the distance of the upstroke. The miner could then step off to a corresponding side platform for the downstroke, and get back on for the next upstroke.
By doing this repeatedly a miner could effectively be lifted to the surface without having to climb a ladder. If there were two side by side pump rods, the journey would be that much faster, as each rod worked in opposite rhythm. In a matter of minutes, a miner could hitch a vertical ride without stepping foot on a ladder. Simple.
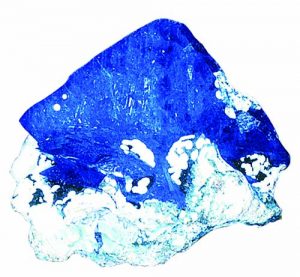
It didn’t take miners long to pass the word, and this pump rod ‘elevator’ became common practice. Unfortunately, there was a hidden problem that reared its ugly head at the Levant mine in Cornwall. After prolonged use, the wrist pin that fastened the top end of the pump rod to the beam engine arm wore out. The sheer weight of the rod, its dewatering load and dozens of miners hanging on, were too much. The wrist pin broke and the entire mechanism, rod, water, and miners plunged down the shaft, killing most of the working hands. Ultimately, science revealed it was not the exhausting climb out of the mine or the cold Atlantic winds that were the cause of miners’ breathing problems. It is, instead, rock dust that causes silicosis of the lungs.
Mining in Cornwall, England’s Influence
All of that is to say the influence of mining in Cornwall, England on the mining industry the world over is obvious. In many cases “Cousin Jacks” ended up in leadership positions at developing districts. Known as mine captains or managers, they would often bring Cornish miners into the district to work.
It is safe to say that the practical knowledge amassed and shared by mining in Cornwall, England and the essential German expertise and information, revealed by George Bauer in his Latin text De Re Metallica, both had a profound influence on worldwide mining and the lovely mineral specimens we admire today.
This article about mining in Cornwall, England and how it impacted the first hard rock mining in America was written by Bob Jones and first appeared in Rock & Gem magazine. Click here to subscribe.